AOI ITO- Seeing What Matters In Manufacturing
Ever wonder about the unseen efforts that go into making the everyday things we use, like your phone or computer? It's pretty incredible, if you stop to think about it, how much care goes into ensuring everything works just right. From the tiny parts that make up a circuit board to the way data gets to us, there's a whole world of systems working behind the scenes to keep things running smoothly and, you know, make sure what we get is top-notch.
For a long time, getting things made perfectly, especially in busy factories, was a real challenge. You had people doing their best, but even the most careful human eye can miss a tiny flaw. This is where something called Automated Optical Inspection, or AOI, comes into the picture, helping to spot those little imperfections that might otherwise slip through. So, it's almost like having a super-powered pair of eyes on the production line, just catching everything.
This technology, which we can loosely think of as a kind of "aoi ito" for quality, has changed how many things are put together. It's not just about finding mistakes; it's about making the whole process of creating stuff more reliable and, in a way, smarter. We'll explore how this kind of inspection system came to be, what it actually does, and how it's shaping the way things are made now and into the future, too, keeping everything on track.
Table of Contents
- The Story of Quality Checks- How Did We Get Here?
- The Early Days for aoi ito in Production
- What Exactly Does an aoi ito System Do for Us?
- Seeing the Tiny Details with aoi ito
- Why Does aoi ito Matter So Much for Certain Industries?
- The Financial Picture of aoi ito Systems
- How Does aoi ito Keep Our Information Current?
- Understanding Information Freshness with aoi ito
The Story of Quality Checks- How Did We Get Here?
If you cast your mind back a bit, say to the years before 2005, the tools used for checking quality in places that put together electronic components in China were, for the most part, from other countries. These imported pieces of equipment, you know, pretty much had the market to themselves. While they certainly gave a push to how the electronics assembly business grew, they also brought along some pretty hefty costs for smaller and medium-sized companies, especially in the short run. So, it was a bit of a balancing act, you might say, helping things move forward but also adding to the financial burden for many.
This situation meant that local businesses had to figure out how to pay for these rather expensive machines if they wanted to keep up with the quality standards that were becoming more and more common. It was a time when getting the right tools for the job often meant looking outside the country, and that, naturally, came with its own set of expenses. The reliance on these outside suppliers shaped the early growth of the industry, too, pushing some companies to find ways to make do or save up for these important pieces of gear.
Over time, as things moved forward, there was a growing desire to have more local options for these kinds of inspection tools. People started to see the benefit of having solutions that were closer to home, perhaps more affordable, and just as effective. This push for local innovation would eventually lead to new developments, changing the way factories approached their quality control, and helping to bring down some of those initial high expenses that were a bit of a hurdle for so many. It was, in some respects, a period of getting ready for what was to come.
The Early Days for aoi ito in Production
The very beginnings of what we now call aoi ito, or automated visual checking equipment, are tied closely to how factories began to really think about getting things right, every single time. This kind of equipment became a part of the bigger picture of visual checking systems used in making things. It was all about making sure that what came off the production line was as close to perfect as possible, which is a big deal when you're making millions of tiny parts. So, in a way, this was the start of a new era for quality control, you know, making sure things were spot on.
This particular method of checking has found its home in a lot of different places, especially where electronic bits and pieces are made. Think about printed circuit boards, those green things with all the lines on them, or the screens on your devices, and even the tiny computer chips that power everything. These are all spots where aoi ito has become a very common sight. It's because these items have so many small details that need to be just right, and missing even one tiny flaw can cause big problems later on, which, you know, nobody wants.
At the current moment, aoi ito is a pretty standard tool in the production of printed circuit boards and integrated circuits. It's a way of making sure that these essential parts are put together without any visible mistakes. The need for such precise checking tools grew as the things we make became smaller and more intricate, demanding a level of accuracy that human eyes just couldn't consistently provide. So, it really filled a gap, allowing for a much higher standard of production quality across the board, which, you know, is quite something.
What Exactly Does an aoi ito System Do for Us?
When we talk about aoi ito, or AOI visual checking equipment, we're really talking about a clever machine that looks for little imperfections on the outside of a product. It's like a super-sharp observer, checking if there are any cracks, if something is a little bit off its intended spot, or if a part is missing entirely. This kind of check is incredibly important because even the tiniest flaw can make a big difference in how something works, or if it works at all. So, it’s basically a very diligent detective for product appearance, which is pretty neat.
The basic idea behind how these machines work is fairly straightforward, though the technology itself is quite advanced. They use camera setups to take pictures of the item being checked. When light bounces off the item, the camera measures how bright that reflected light is, turning it into a numerical value, kind of like a shade of gray. This "gray value" for the item being checked is then compared to what a perfect, standard item should look like. Any differences between the two, you know, might signal a problem.
By comparing the actual item's appearance to a stored image of what's considered "correct," the aoi ito system can quickly figure out if something is amiss. It's a bit like having a perfect blueprint and then checking if the building matches it exactly, brick by brick. This method allows for very fast and very consistent checks, much faster and more reliable than someone trying to do it by hand. It's a way to keep things moving along without sacrificing quality, which is, you know, pretty essential in busy factories today.
Seeing the Tiny Details with aoi ito
These systems are pretty good at picking up on things that are really small. For example, they can tell if a component is just a little bit out of place, maybe shifted by a tiny fraction of a millimeter. They can also spot if a connection on a circuit board is broken, or if a tiny piece that should be there simply isn't. This level of detail is, you know, incredibly important for things like modern electronics, where every single part has to be in its exact spot for the whole thing to function properly.
The way they do this involves some clever image processing. The machine takes what the camera sees and uses special computer programs to analyze it. It's not just looking for a simple match; it's looking for patterns, shapes, and the exact placement of things. If something deviates from the expected pattern, even slightly, the system flags it. This ability to see and interpret such fine details is what makes aoi ito so valuable in keeping product quality high, too, making sure everything is just so.
Think about a very busy production line where thousands of items are being made every hour. Having a system that can automatically scan each one, check for these tiny issues, and do it without getting tired or making human errors is a huge advantage. It means fewer faulty products make it out the door, which saves money and keeps customers happy. So, in a way, aoi ito acts as a silent guardian of quality, making sure the little things don't become big problems, you know, for everyone involved.
Why Does aoi ito Matter So Much for Certain Industries?
Making a single aoi ito machine can be quite an expensive undertaking. For instance, a laboratory platform designed to check silicon wafers, where I happen to work, had hardware costs that went beyond one hundred million New Taiwan Dollars. This gives you a bit of an idea of the kind of investment we're talking about for these systems. So, it's pretty clear that these aren't just everyday tools that any business can simply pick up and use without thinking about the cost, you know, it's a serious commitment.
Because of this rather high price tag, it's really only industries that deal with very large quantities of products and have a high degree of automation that can truly make the most of aoi ito checking. Think about places that make semiconductors, those tiny brains of our electronic devices, or computer chips. These are industries where production happens on a massive scale, with very little human involvement once things get going. They produce so many items that even a small percentage of errors would add up to huge losses, very quickly.
So, for these kinds of businesses, the cost of an aoi ito system, while significant, is actually worth it in the long run. It helps them maintain an incredibly high level of quality across millions of products, which saves them from having to throw away or fix countless faulty items. It's a strategic investment that pays off by preventing problems on a grand scale, ensuring that what they produce meets the very strict standards required for such advanced components, you know, keeping things running smoothly.
The Financial Picture of aoi ito Systems
The financial side of bringing in aoi ito technology isn't just about the initial purchase price. It also involves the savings that come from catching mistakes early. If a faulty part makes it further down the production line, fixing it or throwing away a whole assembled product costs much more than fixing a tiny part at the very beginning. So, in a way, these machines are like an insurance policy against bigger, more expensive problems later on, which, you know, is a smart way to think about it.
Consider the difference between traditional ways of checking, which might involve people looking at things, and what aoi ito does. Human checking can be slow, and it's easy to miss things, especially when you're looking at thousands of tiny details all day. This means more errors slip through, leading to more waste and rework. The automated nature of aoi ito means it can check items much faster and with a much higher level of accuracy, reducing those costly mistakes. It's pretty much a way to make the whole process more efficient, you know, saving time and money.
For businesses that rely on producing things with extreme precision, like those in the semiconductor world, the investment in aoi ito is almost a necessity. It allows them to maintain their reputation for quality and avoid the huge financial hit that comes from mass product recalls or customer dissatisfaction. It's about staying competitive and making sure that every single item they produce meets the highest possible standards, which, you know, is vital for their continued success in a very demanding market.
How Does aoi ito Keep Our Information Current?
There's another interesting idea connected to "AOI," which is "Age of Information," often shortened to AoI. This concept, you know, is all about how fresh or timely the data we collect actually is. It’s particularly useful for situations where getting information quickly and knowing how current it is really matters a lot. It helps us describe just how "new" the data a system has gathered is, which, for many tasks, is pretty important. So, it’s a way of putting a number on how up-to-date our knowledge is, which is quite useful.
Think about situations where you need to make decisions based on what's happening right now, not what happened five minutes ago or an hour ago. For example, if you're controlling a robot arm on a factory floor, you need to know its exact position at that very moment, not where it was a second ago. The AoI concept helps us measure how quickly that information gets from where it's collected to where it's used. It's a way to ensure that the data you're working with hasn't gone stale, which, you know, could lead to problems.
The world around us is constantly generating information, pretty much all the time, everywhere, and in little bits and pieces. If we want to use this information to help us make good choices, we usually have to gather it regularly. So, this idea of checking information age, or AoI, helps us figure out if the data we're using is still relevant enough to be helpful. It’s a way to put a value on how "new" the collected information is, which, you know, is a pretty neat way to think about data quality.
Understanding Information Freshness with aoi ito
A specific measure within this concept is called Peak AoI, or PAoI. This represents the highest age that information reaches before it gets updated. It's like saying, "What's the oldest piece of information we're ever going to use before we get something newer?" This is important because it tells you about the worst-case scenario for how fresh your data is. If your PAoI is too high, it means you might be making decisions based on old facts, which, you know, could be a problem.
The need for this kind of measurement comes from the fact that information is produced all the time, in all sorts of places, and often in a scattered way. We can't always get every single piece of information the moment it's created. So, we usually collect it at regular intervals. The AoI concept helps us understand the timeliness of that collected data, making sure it’s still good enough to assist us in making choices. It’s about keeping a pulse on the information flow, ensuring it’s not too old to be useful, which, you
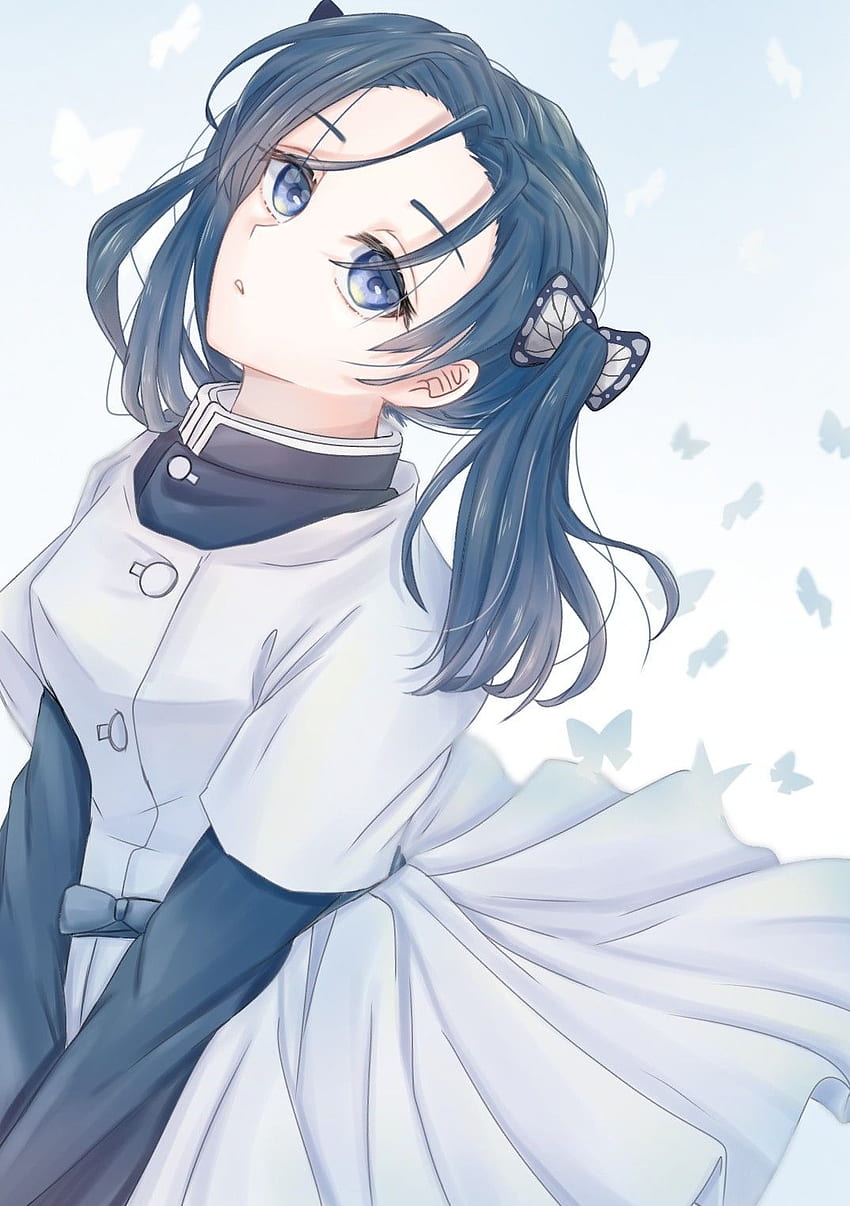
Top hơn 169 hình nền aoi siêu hot - taiminh.edu.vn
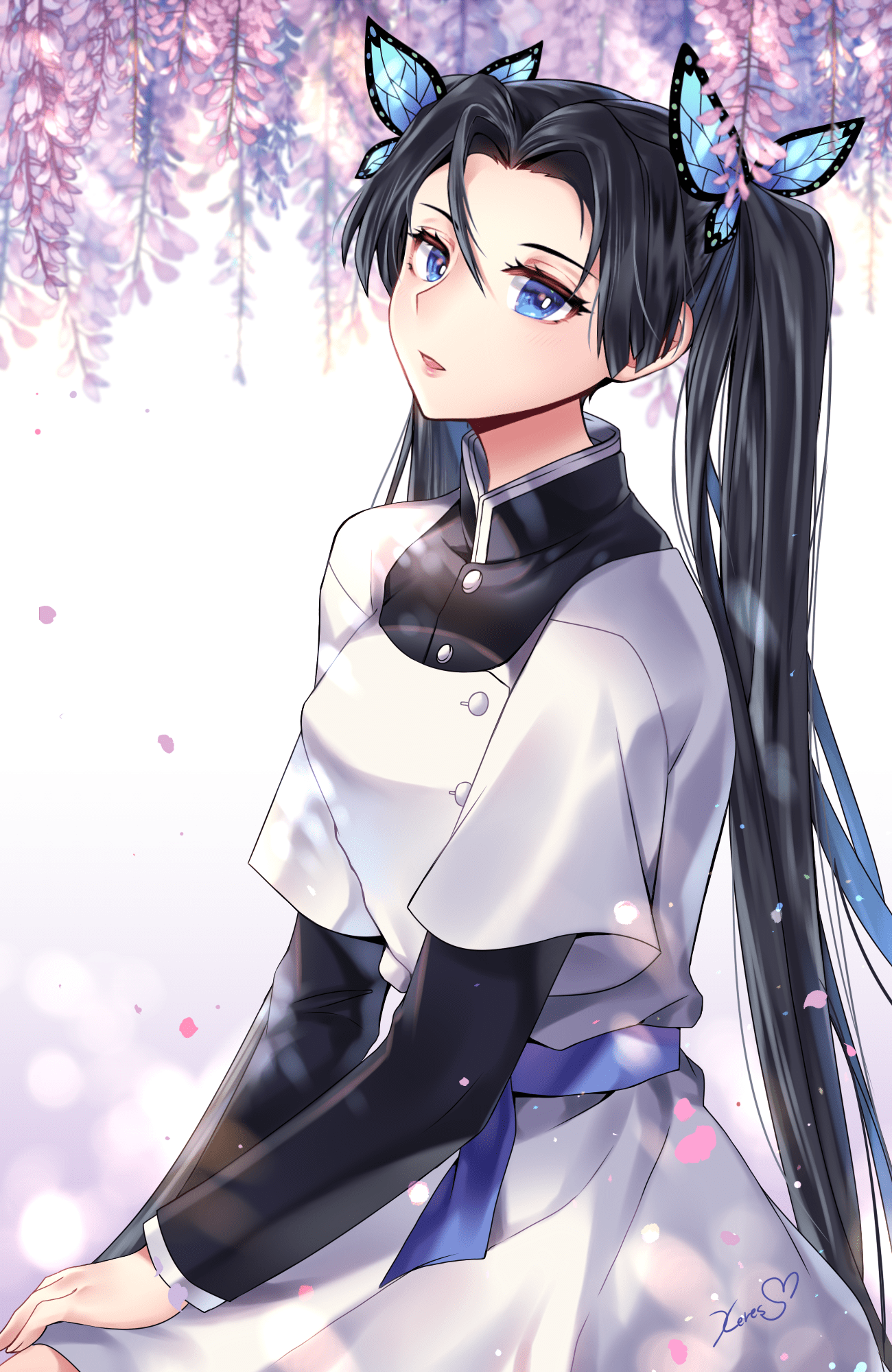
Top hơn 87 về hình nền aoi mới nhất - coedo.com.vn
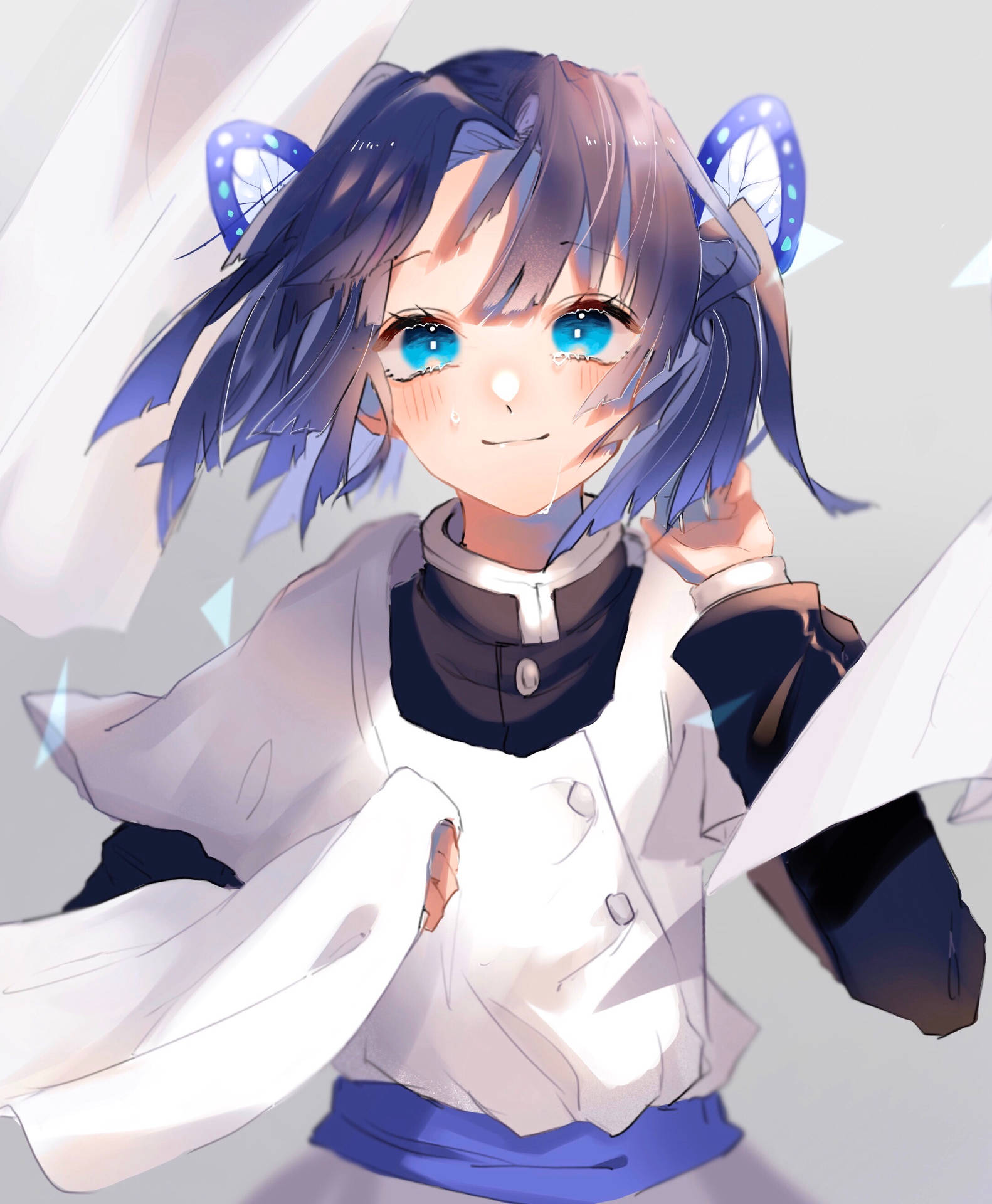
Top hơn 87 về hình nền aoi mới nhất - coedo.com.vn